Технология производства компенсаторов.
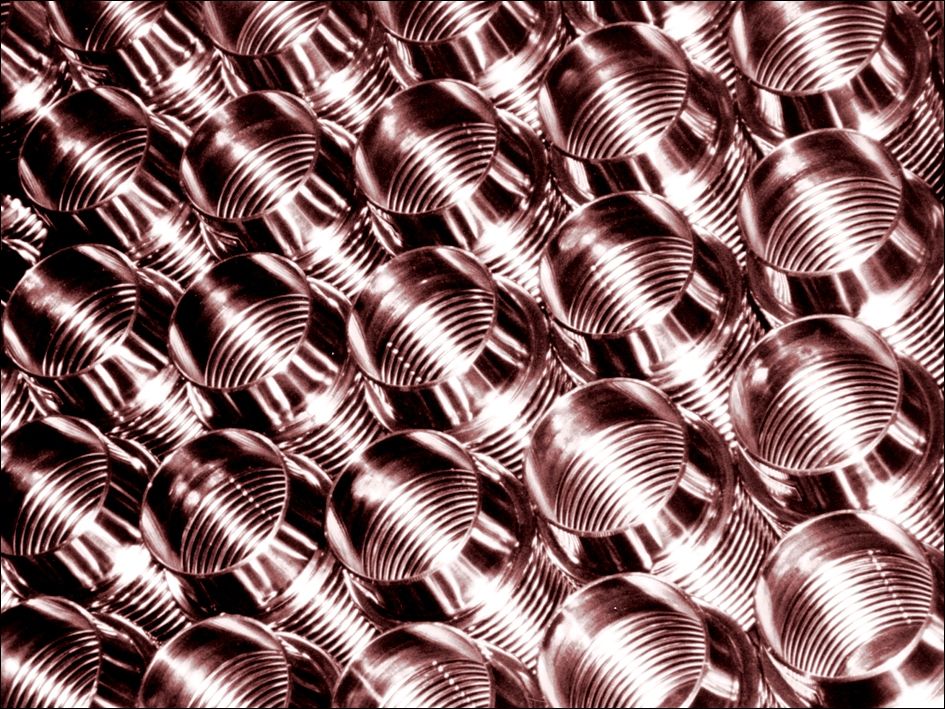
Технология производства компенсаторов заключается в следующем: гофрированная часть компенсатора, число гофр которого определяется заданным рабочим ходом (интервалом компенсации), изготавливается либо методом гидростатического выдавливания (для всех типов компенсаторов диаметром до 1000 мм), либо роликовым формированием-накатыванием (для диаметров свыше 1000 мм).
Исходной заготовкой является многослойный цилиндр из тонкого листа нержавеющей аустенитной стали.
Качество компенсатора определяется:
- величинами отклонений процентного содержания спектра химических элементов стали от марочного их стандарта;
- структурной однородностью (аустенит) используемого тонкого листа из нержавеющей стали;
- технологией сварки (обеспечение стабильности параметров электрической дуги на электродах) при которой коэффициент свариваемости достигается равным еденице (это обеспечивает химическую и структурную однородность в сварном шве и в краях свариваемого листа нержавейки);
- методикой формирования гофров сильфонной части компенсатора (ноу-хау фирм изготовителей) при которой достигается одинаковая (1-1.5%) толщина стенки говра влюбом месте профиля гофра. Обеспечивается, так же, одинаковая твердость гофра по всему его профилю (и для всех гофров сильфонной части компенсатора). Это гарантирует равномерное распределение упругих свойств компенсатора и , следовательно, устойчивость к нагрузкам на растяжение, создаваемым внутренним давлением в трубопроводе, и к внешним нагрузкам на компенсатор, создаваемым температурными деформациями трубопровода.
Испытание компенсаторов
Все компенсаторы в процессе производства проходят строгий технологический отбор и ряд испытаний на прочность и другие параметры. Процесс тестирования компенсаторов представлен на видео.
В процессе испытаний и тестов, образец компенсатора из партии, должен выдерживать нагрузки, превышающие номинальные в несколько раз. Не прошедшие испытания образцы отбраковываются.
На следующих фото представлены результаты потери устойчивости компенсаторов:
Потеря устойчивости складок гофрированной части сильфона
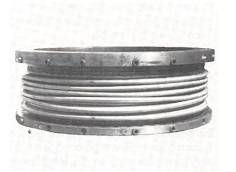
Потеря поперечной устойчивости сильфона при осевом сжатии
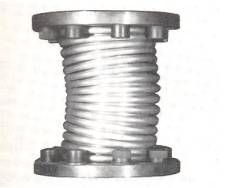
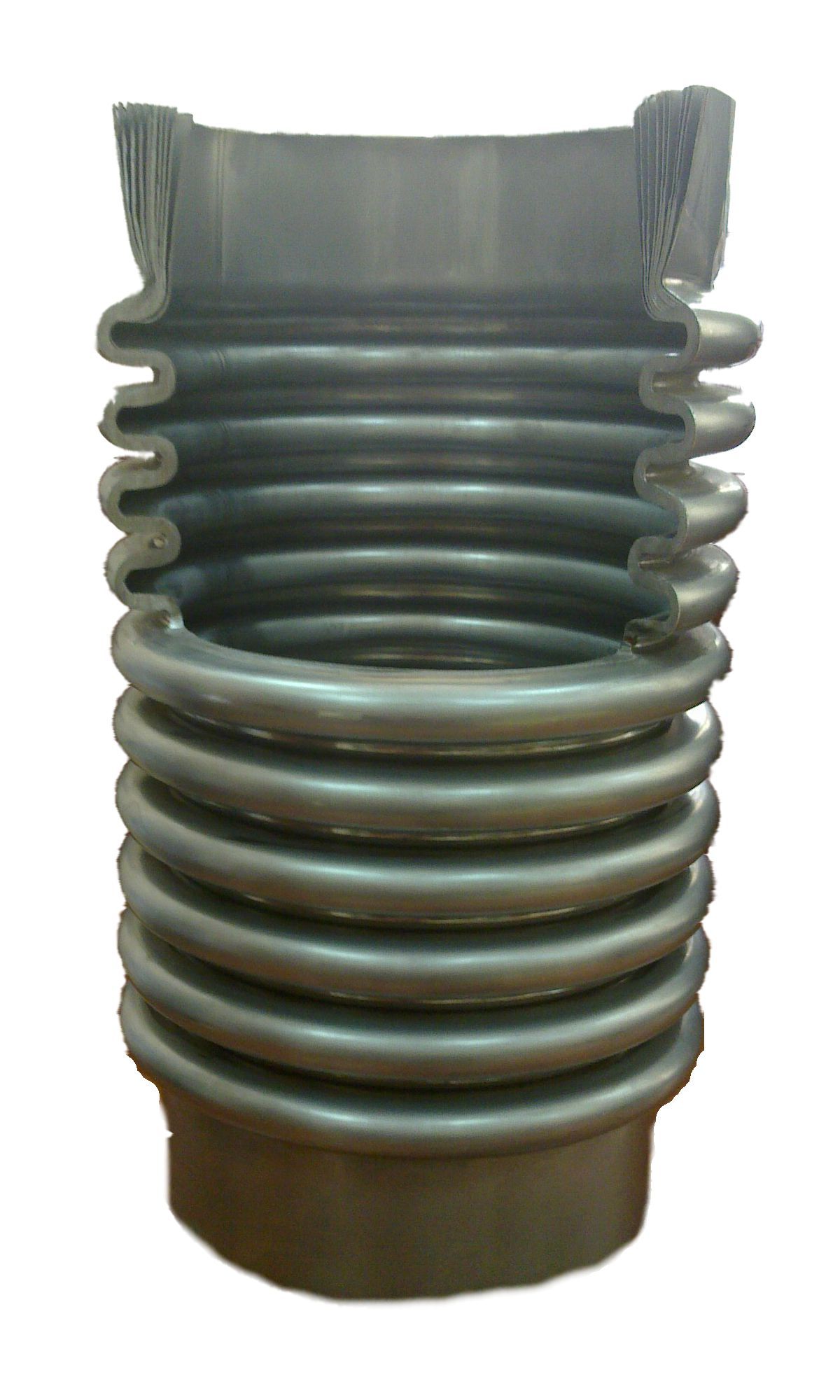
Многослойные сильфоны
Многослойное исполнение сильфона компенсатора является технологическим приёмом по обеспечению элластичности компенсатора и многократному снижению напряжений в металле сильфонной части компенсатора.
Все сильфоны производятся из нержавеющей стали марок AISI 304, AISI 316 и AISI 321. Для высокотемпературных изделий применяются специальные сплавы марок Incoloy 800 и AISI 309. Свертки сильфонов компенсаторов многослойные, при этом число слоев зависит от требований, предъявляемых к компенсатору.
Для создания отклонения (f) в однослойной балке толщиной (s) требуется сила F1
Для создания того же отклонения (f) в двуслойной балке с суммарной толщиной (s/2+s/2=s), требуется сила F1/4
Конструкция заготовки для компенсатора и разрез стенки компенсатора после его формирования приведены ниже:
Заготовка под сильфон компенсатора:
внутренний и внешний герметичные цилиндры и намотанные внутренние слои.
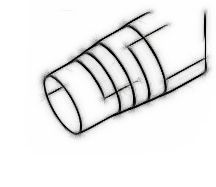
Технология формировании гофров (ноу-хау) такова, что толщина всех слоёв при деформации остаётся одинаковой по всей длине гофра.
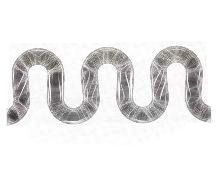
Кроме всего перечисленного, эксплуатационная надёжность зависит от конструкции и качества исполнения сварного соединения сильфона с присоединительными патрубками.
Решение этой задачи проиллюстрировано ниже:
Изгибающие моменты достигают своих максимумов в самой верхней и нижней частях гофра. В средней части (половина высоты профиля) момент меняет знак и,потому, равен нулю. Как раз на этом уровне и осуществляется приварка сильфона к патрубку.
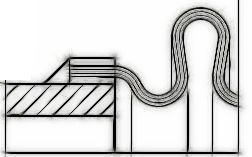
На срезе продемонстрирована реализация разгружающей конструкции соединения в реальном компенсаторе.

Специалисты нашей компании произведут расчет компенсаторов по требуемым Вам параметрам. Звоните (347) 294-17-77, WhatsApp: +7 987 254-17-77 или пишите на электронную почту Адрес электронной почты защищен от спам-ботов. Для просмотра адреса в вашем браузере должен быть включен Javascript.